Covered Anaerobic Lagoon Technology
Pre-Treatment
The palm oil mill effluent (POME) is first conditioned to achieve the necessary parameters to enter the digester. The conditioning process involves screening the POME for larger objects such as dirts or fibres. Then, the POME is neutralized to an optimal pH, which is situated between 6.5-7.5.
H2S Scrubber
The biogas produced from the digester is transferred into the H2S scrubber. The scrubbing process essentially purifies the gas from H2S, a corrosive element that causes severe damage to biogas engine. This optimizes the operation and lengthens the lifetime of the engine, reducing long-term capital expenditure.
Bio-Digester
The palm oil mill effluent (POME) is initially processed through a cooling pond to bring its temperature below 40ËšC as the organisms within are mesophilic (optimal growth at around 37ËšC). Subsequently, the POME is fed into the digester where anaerobic microorganisms digest the mixture and create biogas. To achieve an optimal and continuous production of biogas, a network of pipes and pumps continuously mixes the liquids to ensure homogeny and avoid sedimentation, which is detrimental to biogas production. The digester's parameters are constantly monitored for pH, temperature, total suspended solids (TSS), volatile fatty acid (VFA), and alkalinity to ensure the ideal conditions for a hydraulic retention time of 30 days, which optimizes biogas production.


Dehumidifier
In this step, water is extracted from biogas to prevent condensation, and will serve to optimize the combustion process. A low-moisture biogas (relative humidity below 80%) promotes engine efficiency, which directly translates into fuel consumption savings.

Gas Engine
Following the scrubbing and dehumidifying process, the treated biogas is fed into the engine to produce electricity. A typical engine achieves an electrical efficiency between 36-42%.
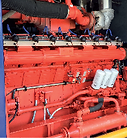